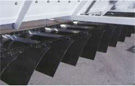 |
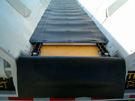 |
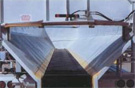 |
Overlapping Chain
and Flap Design
Promotes gripping of product for efficient unloading.
Trailers empty very quickly and safely, producing
a compact pile. Our steel EagleBar crossbars are patent pending
and lead the industry in strength vs. weight. Aluminum bars available. |
Overlapping Chain and
Flap Grips and gently unloads any product. Won't slip in muddy or sloppy conditions like one piece conveyor belts.
|
Plastic Lining
Our low friction plastic liner makes unloading
even quicker and easier. This liner consists of
High Molecular Weight (HMW) plastic on the side
slopes and Ultra High Molecular Weight (UHMW) plastic
on the trailer bottom. These high-quality liners
ensure long life and are especially useful in colder
climates, as well as and when the payload is somewhat
adhesive. They also provide an extremely protective,
abrasive-resistant surface. |
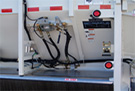 |
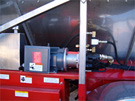 |
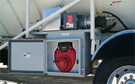 |
PTO Unload
Pressure and return hydraulic hoses are installed
to the front of the trailer with quick couplers.
A variable speed adjustable flow control valve
with gauge allows for easy unloading.
|
Electric Unload System
A 5-h.p. or 7.5-h.p., single-phase, 220-volt electric motor
is directly coupled to a hydraulic pump. A three-phase
electric motor
is optional. |
Gasoline Unload System
We utilize an extremely reliable, long life, 20-h.p.,
electric start gas engine directly coupled to a
hydraulic pump. |
The unloading system is capable of handling up to
35 tons of product. At each end of the body, there
are shaft mounts that are welded to the body. Bearings
are mounted to the front shaft mounts and the front
shaft is installed into the bearings. A lock
collar and set screws on the bearings keep the front
shaft from moving side to side. The front shaft
assembly slides on the shaft mounts forward or rearward
to tighten or loosen the conveyor as needed for proper
tension on the conveyor. Sprockets are welded
onto the front and rear shafts and helps guide the
chain and flap assembly as it pulls the load to the
rear of the body for unloading. They then travel
under the body to begin another continuous loop.
The
rear shaft is inserted into a speed reducing planetary
gearbox. This
assembly is then bolted to the rear shaft mounts. The shaft is kept from
moving from side to side by a lock collar and set screws on the bearing. The
speed reducer is a heavy-duty gearbox that amplifies the rotating force supplied
by the hydraulic motor, which is bolted to the speed reducer. The speed
reducer supplies the substantial amount of torque necessary to move a conveyor
loaded with up to 35 tons of product and to discharge the load out the rear of
the body. Hydraulic power is supplied by an electric motor and/or gas motor
driving a hydraulic pump mounted on the side of the body and/or a PTO driving
a hydraulic pump on the truck. The operator controls the speed at which
the conveyor moves, which speed ranges from 0 ft/min to 40 ft/min. The conveyor
controls are located on the sloped sidewall of the body.
Plastic lining is bolted
to the floor and sidewalls of the body. Two
or three (depending on application) high tensile-strength
steel pintle chains are then placed parallel to each
other on top of the plastic floor liner. These
chains run the length of the body and are connected
to each other by crossbars constructed of steel channel,
steel tubing or aluminum. The chains, which
are guided by the sprockets in the front and rear
of the trailer body, loop under the body to create
a continuous conveyor. Attached to the crossbars
on the leading edge are overlapping flaps made of
tough, flexible pieces of conveyor belting. They
overlap each other to make a continuous segmented
conveyor. The
length of the crossbars (distance between the chains)
depends on the desired width of the belt. The
trailer bodies are manufactured in six belt sizes:
25”, 31”, 36”, 41”, 48”,
and 61”.
The product is moved to the rear of
the trailer body and unloaded through the door opening. A
variety of door options accommodate metered and unmetered
unloading and many are capable of opening fully to
unload the product. An
AG Bag attachment is offered and designed for products
such as distillers mash, a feed product that cannot
be exposed to air for prolonged periods of time. The
AG Bag attachment enables the distillers mash to
be unloaded directly into bags for storage. Another
option, the grain transition funnel, enables grain
to be unloaded directly into augers. |